When you come to solder a battery / ESC leads to a Deans socket & plug assembly it’s often found to be a little difficult for a couple of reasons.
1/ How to hold the plug or socket in place while soldering the leads,…and
2/ Sometimes the plastic that forms the bulk of the plug / socket goes a bit soft due to the heat being used to solder the wires to relatively large connector pins. (You have to get the pins up to a reasonable temperature to allow the solder to ‘take’ to them.) This softening of the plastic can allow the pin / socket to move out of alignment so when you try to fit the plugs together again, after you’ve attached the cables, the dam things wont fit together!!! :!:
The solution that I use is:-
a/ To hold the deans plug in a pair of pliers or grips with a elastic band around the handle to maintain grip on the plugs. (as shown)
b/ To stop the connector pins / sockets from moving out of alignment due to the plastic getting soft…..Fit the male and female plug parts together before you start soldering. That way they will always remain aligned.
Whether you get the problem of the pins not aligning, after you’ve soldered the cables, really depends upon your soldering skills. Speed is the key, but being able to make a good joint quickly is easier said than done! So keeping the male and female parts together helps to alleviate the problem of possible miss-alignment.
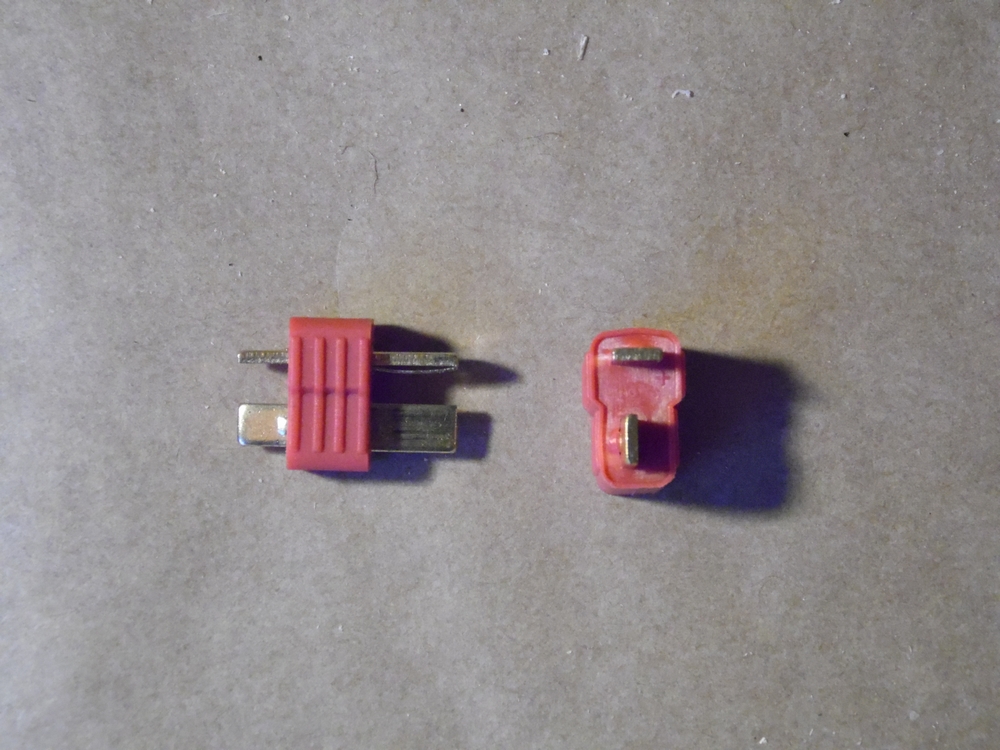
K.